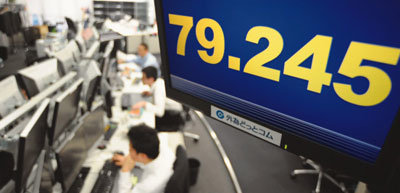
엔고 현상이 절정으로 치닫던 2011년 10월 31일 일본 도쿄 한 은행 딜링룸에서 직원들이 외환업무를 처리하고 있다. 이날 오전 엔화 값은 오세아니아 외환시장에서 달러당 75.32엔으로 사상 최고치를 기록했으나 일본 당국의 시장 개입 직후 79엔대로 급락했다.
현재 일본 기업들의 채산성 환율(기업이 채산성을 확보할 수 있는 환율)은 1달러당 83엔으로, 이보다 12% 이상 낮은 95엔 전후의 엔저 상황은 기업들이 수익을 올리기에 매우 용이한 환경이다. 그러나 단순히 엔저를 부러워하고 말 일은 아니다. 오히려 눈여겨봐야 할 것은 채산성 환율 수준을 지속적으로 개선해 자신들에게 불리하기 짝이 없던 엔고 상황을 극복하려고 일본 주요 기업들이 전략적 대응을 다양하게 시도해왔다는 점이다. 이는 분명 우리 기업에도 시사하는 바가 크다.
한국과 일본 기업들은 수많은 분야에서 경합한다. 과연 일본 기업들이 엔고 시기에 축적한 힘을 앞으로 어떻게 활용해나갈지, 그간 일본 기업들이 어떤 노력을 기울여왔는지를 검토하는 것은 우리 기업들의 미래를 위해서도 중요한 일일 수밖에 없다. 주지하다시피 이제는 우리 기업들이 ‘엔저원고’라는 불리한 상황에 놓인 까닭이다.
차별화된 생산기술
최근 엔저 전환은 우리 기업과 일본 기업의 가격경쟁을 한층 격화할 수밖에 없고, 한국 기업이 크게 불리한 위치에 놓인 것은 의심의 여지가 없다. 리먼브라더스(리먼) 쇼크 이후 엔고 시기에 한국 기업이 LCD TV, 자동차, 리튬이온 2차 전지 같은 분야에서 점유율을 높여 양국 기업 사이에 역전이 벌어지기도 했지만, 이 같은 한국 기업의 대일 경쟁력 강화 추세가 이번 엔저 현상으로 약해질 우려가 있는 것이다.
특정 국가의 통화가 비싸지면 해당 국가 기업들은 높은 원가 압박에 시달리게 된다. 엔고 또한 일본 기업의 생산비용을 상승시키는 요인으로 작용했고, 그에 따라 수출품 가격이 올라 매출이 줄어드는 악순환에 시달려야 했다. 전통적으로 일본 기업들이 이러한 압박에 대응해 활용하는 대표적인 전략은 원가 절감이었다. 잔업시간을 줄이고, 임금인상을 억제하며, 각종 경비를 절감하는 식의 합리화에 매진했던 것이다.
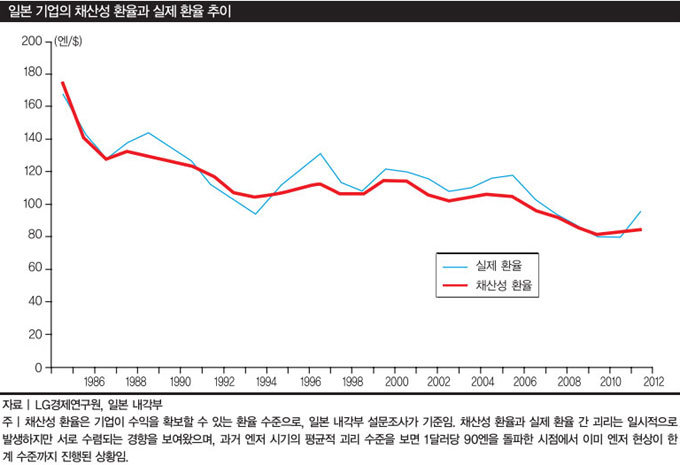
자동차 기업 도요타의 경우를 보자. 도요타는 각종 낭비를 억제하는 경영체질 강화대책을 오랜 기간에 걸쳐 강구하면서도 고도의 생산기술을 축적해 일본 내에서 생산 공장을 유지하는 데 성공했다. 도요타는 엔고와 동일본 대지진 여파에도 일본 내 생산능력을 연간 300만 대로 유지하겠다는 전략을 고수하고 있다.
이를 위해 고객 주문량에 따라 생산량을 감축해도 수익성을 확보할 수 있도록 생산설비를 소형화하고 설비투자 부담을 절감하는 일에 주력했다. 예를 들어, 각종 부품의 금형 크기를 1/2에서 1/10까지 줄여 설비투자비용을 40% 절감한 것이다. 최근에는 자동차의 디자인 자유도를 높이면서도 각 차종 간 공통 부품이나 유닛을 사용해 비용을 줄이는 모듈형 생산시스템을 TNGA(Toyota New Global Architecture)라는 이름의 전략으로 추진하고 있다.
일본 기업들은 생산기술을 연마하는 과정에서 가공 공정이나 설비 개선뿐 아니라 재료 자체의 혁신도 모색했다. 소재와 부품, 장비, 제품에 이르는 수직적인 기술력을 통해 전체적인 기술혁신 능력을 제고하는 교세라가 대표적 사례다.
해외 거점? 창조성을 활용하라
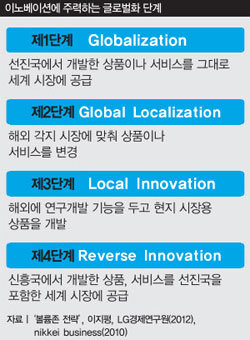
한때 일본을 대표하는 오디오 기기 브랜드였던 아이와(AIWA)의 경우, 단순 조립 거점을 순차적으로 국외로 이전하면서 해외 생산 비율이 1985년 10%에서 99년 89.9%로 높아졌다. 그러나 2000년대 들어 수익성이 급격히 악화돼 모기업인 소니가 사업을 흡수했고, 2002년에는 결국 회사가 소멸됐다. 제조기능을 단순히 이전하는 방식으로는 현지의 노동임금이 상승하거나 현지기업이 성장하는 등의 사업환경 변화를 극복할 수 없었기 때문이다. 요컨대 차별화된 경쟁력을 유지하는 일이 불가능했던 것이다.
반대로 생산 거점 해외 이전으로 성과를 거둔 일본 기업을 보면, 본사 공장과 해외 공장의 조직 능력을 연계 발전시켜 글로벌 네트워크로서의 차별적 가치와 경쟁력을 강화해왔다는 사실을 알 수 있다.
이러한 기업들은 초기 생산 거점 이전 단계에서는 본사가 집중적으로 현지공장에 기술과 노하우를 지원했지만, 단계적으로 현지화를 이루고 현지의 제품개발이나 연구개발 능력을 강화해 해외 거점의 생산기술력을 연마하는 방식을 택했다. 또한 해외 거점에서 개발한 성과를 본사에 피드백해 다른 해외 거점에서도 활용하게 만드는 이른바 ‘리버스 이노베이션(Reverse Innovation)’ 체제를 구축하기도 했다. 예를 들어 닛산의 경우, 태국 등 아시아 거점의 인력을 활용해 흔히 ‘볼륨존(Volume Zone)’이라 불리는 신흥국 중산층 시장을 겨냥해 소형차 ‘마치’를 개발, 범아시아 시장 공략에 성공한 바 있다.
세계 최대 타이어 제조업체인 일본의 브리지스톤도 미국, 유럽 등지에 연구 거점과 대규모 주행시험장을 운영하면서 현지시장을 겨냥한 제품 개발에 주력한다. 유럽에서는 고속도로 운전을 즐기려는 소비자를 위해 고속주행 시 안전성과 핸들링을 고려한 타이어 개발에 주력하고, 미국에서는 현지 소비자가 요구하는 안정적 내구성을 강조한 타이어를 개발하는가 하면, 중국에서는 열악한 도로 사정에 적합한 타이어를 개발하는 식이다. 나라마다 다른 고객의 구매 선호 포인트에 맞게 제품을 개발하는 데 현지 거점의 창조성을 활용하는 셈이다.
강점 기술에 글로벌 마케팅 결합
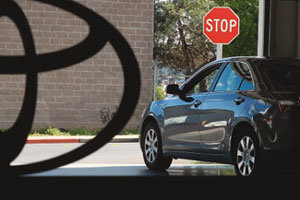
엔고 현상에 동일본 대지진 등이 겹쳐 한때 제너럴 모터스(GM)에 차 생산 1위를 내주기도 했던 도요타는 성공적인 대응 전략으로 위기를 넘긴 대표적 사례로 꼽힌다.
일본 화학기업 중에는 자사의 강점 기술을 기반으로 독창적인 경쟁력을 강화하는 한편, 세계 시장을 제패하는 마케팅으로 성공적인 사업 역량을 갖춰 이른바 ‘온리원+넘버원(Only1+No.1) 기업으로 도약한 사례가 적지 않다. 이들 기업은 엔고나 세계 경기 변동으로 일시적인 어려움을 겪기도 했지만, 중·장기적으로 꾸준한 성장세를 유지해왔다는 특징을 갖는다. 엔고에도 자사의 핵심 역량을 지속적으로 강화하고 이를 글로벌 마케팅과 연계하는 전략이 효과를 거둔 것이다. 한 예로, 신에츠화학의 경우 세계시장 점유율이 40%에 달하는 실리콘웨이퍼, LCD용 포트마스크 기판 등에 주력해 미쓰이화학이나 스미토모화학 같은 종합화학 기업을 능가하는 실적을 기록해왔다.
물론 이처럼 ‘온리원+넘버원’ 기업이 되기 위해서는 엔고 상황 같은 위기를 돌파하는 능력이 중요하다. 후지필름 또한 엔고와 함께 주력 사업인 필름 시장 규모가 2000년대 들어 1/20로 축소되는 시련을 겪었지만, 이를 유연하게 넘어서는 경영능력을 선보였다. 사진 필름 시장을 도태시킨 정보기술(IT) 혁명을 피하지 않고 오히려 적극적으로 활용하는 방향으로 선회해 LCD 필름 개발에 주력하는 한편, 자사의 필름 기술에서 축적한 미립자 가공기술(사진 필름은 20미크론 수준의 작은 폭에 감광 미립자 등 20개가 넘는 미립자를 균등하게 도포해 제조)을 이용해 헬스케어 분야를 개척했다. 미세 가공기술로 축적한 콜라겐 가공 능력, 항산화물질 가공 능력, 나노 레벨의 피부 침투 능력 같은 기술을 갈고닦아 피부노화를 억제하는 화장품을 개발한 것이다.
이렇듯 그간 일본 기업이 엔고 상황을 극복하면서 보여준 전략이나 성과를 살펴보면, 우리 기업들이 원고 현상을 극복하기 위해 매진해야 할 경영전략이 무엇인지 그 방향을 가늠할 수 있다. 먼저 생산기술의 끊임없는 진화가 가장 결정적 포인트다. 안이한 아웃소싱이나 생산 거점 해외 이전 같은 단순한 대안을 떠올리기 전에 생산기술 연마를 통해 국내 공장의 생존 능력을 높이는 노력이 중요하다. 이 과정에서 자사의 핵심 기술을 좀 더 명확하게 만들고 고도화하면 제품을 고부가가치화하거나 신규 분야를 개척하는 등 주도적 대응이 가능해지기 때문이다.
물론 당장 수익이 나지 않는 분야에도 역량을 쏟아부어 10년, 20년 후에나 꽃피울 수 있는 신사업을 육성하는 일본 기업의 경영방식을 한국 기업이 그대로 따라잡기에는 경영 문화나 조직 능력 면에서 쉽지 않은 게 사실이다. 따라서 글로벌한 시각에서 인수합병을 추진해 강점 분야를 심화하는 전략도 중요할 것이다. 원고 현상을 역이용하면서 자사의 기술적 우위를 강화하는 방향에 맞게 기업을 매수하는 기술 지향적 인수합병 전략이다. 국내적으로도 산학연계 같은 비즈니스 생태계를 기술거래 시장이나 인수합병 시장의 활성화로 이어지도록 하는 정책적 노력이 필요하다.
마지막으로 우리 기업들은 생산기술 혁신이나 고부가가치화를 글로벌 경영이라는 시각에서 추진할 필요가 있다. 본사의 기술력과 각 해외 거점의 아이디어를 서로 융합해 높은 기술이 뒷받침하는 고부가가치 제품을 창조해야 하는 것이다. 여기서 유의해야 할 점은 일본 기업의 ‘온리원+넘버원’ 전략이 주는 교훈이다. 단순한 기술 중심 혹은 생산 중심 사고로는 한계를 넘어서기 어렵다는 것이다. ‘온리원+넘버원’ 전략은 마케팅과 글로벌 역량을 동시에 강화할 때만 비로소 성과를 맺을 수 있는 목표라는 뜻이다.