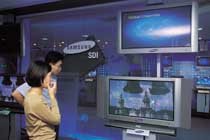
PDP는 플라즈마 디스플레이 패널(Plasma Display Panel)의 약자로 플라즈마라는 고압 방전방식을 이용해 가시광선을 만든 뒤 이를 이용해 영상을 만드는 신개념 영상매체다. PDP는 두 장의 얇은 유리기판 사이에 혼합가스를 주입하고 고전압을 가해 발생한 이온가스를 방전시켜(플라즈마 현상) 화면을 구성한다(그림 참조). 이런 방식으로 동급 브라운관 TV보다 두께는 10분의 1, 무게는 3분의 1 수준으로 줄일 수 있기 때문에 초대형 TV에는 안성맞춤이다. 또 40~63인치까지의 대형인데도 두께가 7~10cm에 지나지 않아 벽에 걸어놓고 볼 수 있다는 장점이 있다.
부품, 제조장비 국산화 전력투구
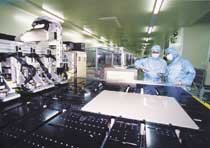
크기를 키우는 것도 화질을 유지한 상태에서 1인치를 늘리기 위해서는 현재 70~80단계나 되는 제조공정을 수없이 반복해야 하는 만큼 단기간에 가능한 것으로 보이지 않는다. 결국 제조장비나 부품을 얼마나 국산화하고 가격과 마케팅 경쟁력을 높이는지가 일본과의 경쟁에서 승리할 수 있는 관건이라는 말이다. 현재 PDP 제조에 쓰이는 대형 유리나 자외선을 받아 발광체 역할을 하는 형광체 등 핵심부품 등은 대부분 일본에서 수입해 사용하는 형편이다.
삼성SDI PDP 판매팀 김하철 상무는 “부품 국산화율만 높일 수 있다면 니콘이나 야시카 등 기존의 카메라 브랜드들이 디지털 카메라 등장 이후 소니나 NEC 등 디지털 기술이 앞선 업체들에게 시장을 몽땅 내어준 것처럼 PDP 시장 역시 국내 업체들이 시장을 장악할 수 있을 것이다”고 전망했다.
그러나 아직까지 일본 업체들과 대등하게 경쟁하기 위해 풀어야 할 과제도 적지 않다. 삼성 SDI에 기술 자문을 하는 서울대 황지웅 교수(전기공학)는 “원천 기술과 관련한 대부분의 특허를 일본 기업과 미국 기업이 갖고 있는 만큼 세계 시장에서 일본과 경쟁하기 위해서는 국내 업체들이 더 큰 노력을 기울여야 한다”고 지적했다. LG전자 관계자도 “20~30년쯤 앞선 일본을 어깨 너머로 배울 수 있던 브라운관 분야와 달리 PDP 기술은 처음부터 끝까지 자체 해결할 수 밖에 없는 상황이다”고 말했다.
업계에서는 국내 업체들이 PDP TV 제작에 필요한 패널뿐 아니라 이를 TV 세트로 조립하는 능력을 겸비하였다는 점이 일본과의 경쟁에서 유리하게 작용할 것이라고 내다본다. 삼성의 경우 과거 TV용 브라운관을 생산해 온 삼성SDI가 PDP 모듈을 만들고 삼성전자가 TV 세트, 스피커 등 주변기기를 조립해 완성한 뒤 삼성전자 상표를 붙여 시장에 내놓는 방식이다. 지난 94년부터 PDP 분야에서 연구 개발을 추진해 온 LG전자는 PDP 모듈과 TV 세트를 한꺼번에 양산하는 체제를 갖추었다.
반도체나 TFT-LCD도 일본보다 늦게 세계시장에 뛰어들어 결국은 일본을 추월한 뒤 세계 최강으로 떠오른 분야. 따라서 PDP-TV에서도 똑같은 대역전극을 연출할 수 있을지에 관심이 모아진다.
반도체나 TFT-LCD와 비교하면 유리한 측면도 있다. 세계시장 진입 시점이 일본과 1~2년밖에 차이 나지 않고, 일본과 달리 ‘G7 프로젝트’에 포함되어 산·학·연 합동으로 우수한 기술 인력을 속속 양산하고 있다는 것. 이들이 바로 우리 수출의 차세대 주력군으로 PDP-TV의 경쟁력을 결정짓는 인적 자원의 보고라 할 수 있다. 이들이 주전 선수로 뛸 한-일간 ‘PDP 대전’의 휘슬은 이미 울린 셈이다.